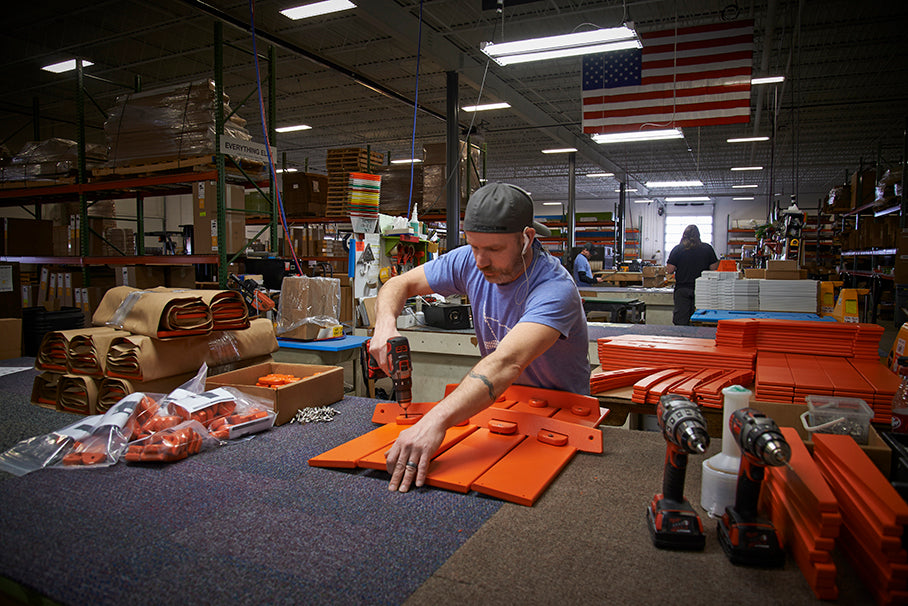
You may know that we manufacture our products from sheets of recycled plastic – primarily from single-use milk jugs. But how does it go from a big sheet to a modern Adirondack chair?
Read on, friends. In this post, we’re going to walk you through the production process – from plastic sheet to Loll chair.
All Loll furniture starts as 4-foot by 8-foot sheets of recycled high-density polyethylene (HDPE), one of the most commonly used plastics in the U.S. Our material is sourced primarily from single-use milk jugs. Our material is received into our facility in bunks, sorted by color. Each bunk includes around 20 to 25 4-foot by 8-foot sheets. We use three thicknesses of material: 1/2 inch, 5/8 inch, and 1 inch. There is a thin film applied to each sheet exterior that protects the material from being scratched during transit. This film is removed in the assembly process.
The process starts with design. Below is Jeff, one of our designers. He uses CAD technology to create renderings of our furniture.
Our manufacturing schedule adheres to lean manufacturing processes. This means all products are made to order – we do not keep an inventory. Orders are organized by like color, like sheet thickness and ship dates. Using the files Jeff designs, our CNC (computer numerical control) files processor Bill programs, or ‘nests’, individual pieces of furniture to get the best yield out of each sheet of recycled material. Once these files are programmed, they are sent to one of our three CNC machines.
The CNC machines read the 3D design files Jeff and Bill create and cut the recycled plastic sheets into furniture components.
After the CNC machine cuts the furniture components, we strip the excess poly. (Think about making cookie cutouts – you always end up with extra dough after you’ve stamped the rolled-out dough. Same deal here.)
Rather than sending this waste to a landfill, we ship it to a recycling plant in Minnesota that processes the scrap commodities to make agricultural drain piping. You can read all about our recycling process in our previous blog post. Loll recycles around 30,000 pounds of waste each month.
The furniture components are then individually hand routed by our operators to create smooth edges that match the side the CNC machine cuts. (The machine only provides roundover on one side.)
The furniture components are then sent to our inspection/insert area.
Each product part is first inspected by our production team and sorted based on orders. Because all of our fasteners are hidden, an aluminum insert – to which a stainless steel bolt will eventually be inserted to – is inserted in this part of the process.
After the product has been sorted and inserted, the furniture pieces are grouped into order-specific pallets and transferred to assembly.
At assembly, our team thoroughly inspects each product again and packages it for shipping. The majority of our products ship flat-packed to save on costs and resources; however, we do pre-assemble some components. We strive for our packaging to be as minimal and efficient as possible, all while ensuring little or no damage during the transit process. Loll continuously works to improve our packaging materials to have the highest recycled content as possible.
All Loll orders ship flat or knocked down. Shipments include either a Loll Tool or an Allen Wrench to aid the assembly process. Assembly instructions and videos may be viewed online prior to receiving.
Time to ship! Boxes are stacked on pallets and prepared for FedEx delivery.
There you have it folks – from a piece of recycled plastic to a modern outdoor lounge chair. The final step looks a little something like this:
Stay tuned for a post to come about the milk jug recycling process – how the milk jug you bring out to the curb is transformed into a usable piece of plastic we make furniture from.